
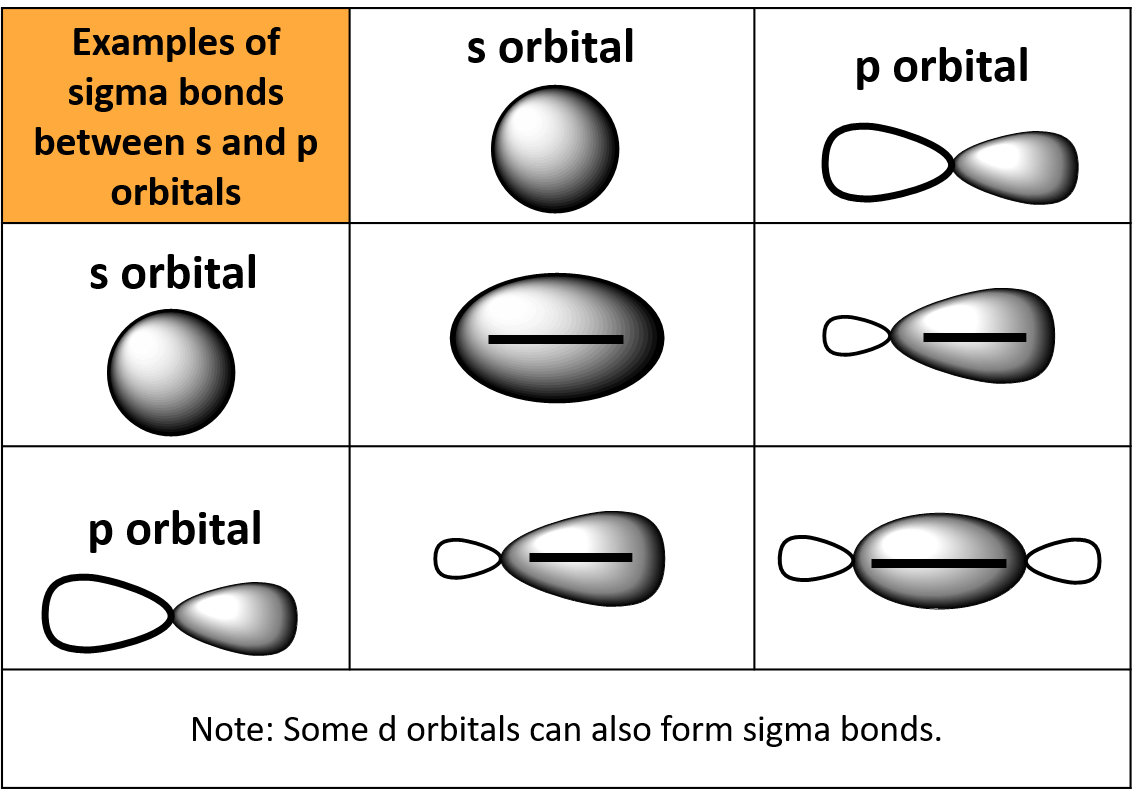
Because the non-normal distribution has a different, non-normal shape, the limits end up either greater or less than 3 sigma limits. With a non-normal distribution, limits are also set to enclose 99.73 percent of the distribution. With a normal distribution, 3 sigma limits enclose 99.73 percent of the distribution. Even when the process is in control, the two estimates of sigma will differ slightly they're only estimates.Ī final factor can cause the limits to differ:ģ) Histogram capability limits can be based on a non-normal distribution. When the process is out of control, the two sigmas can differ dramatically. When a process is in control, there's no "between subgroup" variation and is equal to. Therefore when "between subgroup" variation occurs, it's signaled by out of control points. The histogram limits include the total of both "within subgroup" and "between subgroup" variation:Ī control chart uses only "within subgroup" variation to set limits. In this example, the process sigma level for a specification limit of 31 seconds is: Z (SL ) /. Given the specification limit, SL, the process sigma level, or process Z, is: Z (x ) / (SL ) /. Control charts use average subgroup Range (or average subgroup standard deviation) to capture only the "within subgroup" variation. The one-sided defect rate is applicable to any capable process with 1-sided or 2-sided SLs, even at a 3-sigma level. This doesnt depend on the distribution of the original measurements, just on fourth and second moments. Histogram limits use the sample standard deviation in order to capture all of the variation. This is derived in various places - for example, a reasonably simple derivation is given here. The relationship between sigma of the individual measurements and sigma of X is:Ģ) Different estimates of sigma are used for the histogram and the control chart. The control chart limits use sigma of whatever is being charted, usually X, the mean. The unasked question is "sigma of what?" The histogram limits use sigma of the individual measurements. Still, two main factors produce confusion:ġ) Both are "3 sigma" limits. The limits are used for different purposes: Histogram limits evaluate process capability, Control Chart limits separate common variation from special variation. I think all flight passengers would agree that a flight delay is less worrisome than a flight incident on landing.One of the seemingly deep mysteries of SPC (and often-asked questions for NWA Technical Support) concerns the relationship between Histogram 3 sigma limits and Control Chart 3 sigma limits. Not all opportunities and defects are created equal. In the United States alone if the sigma level were between 3 and 4, there would be 50 newborn babies dropped per day and 5,000 incorrect surgical procedures per week. Number of telephone disconnections Įrroneous business orders Įlectricity outage Number of empty coffee pots at work (who didn’t fill the coffee pot again?) Number of aircraft takeoff or landing incidents It’s one thing to see the numbers and it’s a whole other thing to see how it would apply to your daily life.

What Would Sigma Values Look Like In The Real World? Yield (or Produced or Delivered) Correctly (%) Sigma Performance Table Sigma Performance Levels – One to Six Sigmaĭefects (or Errors) Per Million Opportunities (DPMO) When learning about Six Sigma, it may help to consider these charts, which detail how sigma level relates to defects per million opportunities (DPMO), and some real-world examples.
